コラム
2023/09/01
レーザー切断
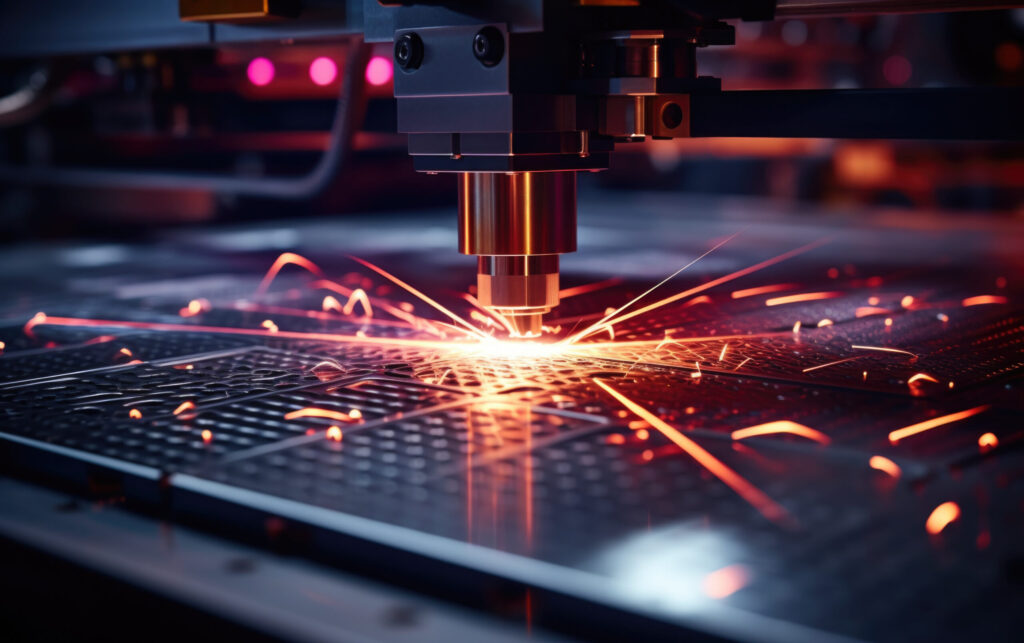
レーザー切断
レーザー切断は、対象物をレーザー光で切断する革新的な加工方法です。
レーザー発振器から出力されたレーザー光を集光し、対象物を溶解させることで切断を行います。さらに、アシストガスを使いながら切断を行うことで、高品質な仕上がりを実現します。また、レーザー切断は難素材の加工にも非常に適しており、金属やセラミックス、樹脂、複合材などさまざまな素材の切断が可能です。
本記事では、レーザー切断の原理や概要について解説します。実際のレーザー切断の実例も紹介しますので、是非ご覧ください。
レーザーによる切断加工
レーザー切断は、レーザー光を利用して対象物を切断する加工方法です。レーザー光は高エネルギーの光線であり、そのエネルギーを利用して切断対象物を溶かすことで切断を行います。
レーザー光は非常に細く密度の高い光束であり、高い精度で切断が可能です。レーザー光が局所的に照射され、溶融された素材をアシストガスで吹き飛ばすので、熱影響が少なく、切断面はきれいに仕上がるのが特徴です。
1)レーザー切断の原理
レーザー切断は、レーザー発振器から反射鏡などを用いて伝送されてきたレーザビームを集光レンズで細く絞って切断材料に照射します。そうすることによって、部分的に溶融させます。またレーザーと同軸に配置したノズルからアシストガスを噴き付け、溶融物を噴き飛ばすことで狭い溝幅の高精度な切断を行います。
2)レーザー切断の利点・欠点
一般的なレーザー切断は、ガス切断やプラズマ切断など従来の熱切断法の一つとして位置づけられます。ただし、従来の方法とレーザー切断を比較すると、レーザー切断には適切な設備と技術が必要なケースや、光源をはじめとして装置自体が非常に高価であるという課題があります。
しかしながら、特に難素材加工や高品質加工の分野ではレーザー切断の普及が著しく、この普及を支える背景には、装置価格に見合ったレーザー切断のパフォーマンスがあります。
レーザー切断の利点としては、仕上がりが綺麗であり、自動化がしやすいということもあります。レーザー切断は、さまざまな産業分野で利用されており、より高品質な金属加工や製造の効率化に貢献しています。
レーザー切断の主なメリットは、以下のようになります。
- 熱の影響が少ないので、熱変形が極めて小さく切断精度が向上
するため、します。変形しやすい薄板の精密な切断は、得意分野と言えるでしょう。 - レーザーの照射は局所的に金属を溶かし、溶融部はアシストガスによって取り除かれます。そのため、切断幅はレーザーの集光径と同程度
にのごく狭い幅で切断できます。 - 高パワー密度ビームを利用する加工は、溶融および溶融金属の除去が迅速で、従来の切断法に比べて切断速度が速い特徴があります。
- 非接触の切断なので、部品の交換は必要なく、レンズやミラーなどの消耗部品の劣化による交換頻度も、接触除去加工に比べて少なくなります。
- 切断箇所の酸化が少なく、加工後の錆の発生や素材の変質を抑えられます。そのため、切断後の仕上げ加工を省略でき、後工程へのシームレスなプロセスを図れます。
- 薄板の切断にはパルスタイプのYAGレーザー切断、厚板には連続発振タイプのCO2レーザー切断の使い分けが一般的ですが、レーザーの種類によって多様な板種・板厚の切断加工に応用できます。ただし従来の手法と比較して、レーザー切断できる板厚には限度があります。
レーザー切断の実行
「レーザー切断システムの構築」や「切断加工に適したレーザー」、「レーザー切断を実行する際の注意点」について解説します。
1)レーザー切断システムの構築
レーザー切断システムの構築には、いくつかの装置が必要です。
まず、切断エネルギーの供給源であるレーザー発振器が必要です。一般的なレーザー切断では、ファイバーレーザー、YAGレーザー、CO2レーザーなどが使用されます。
次に、光学系が必要です。光学系は、レーザー光を集光し、照射ユニットから対象物に正確に照射する役割を果たします。近年ではファイバーを用いて、より柔軟に導光できるようになっています。
また、アシストガスも必要です。アシストガスは、レーザー光と同軸に取り付けられたノズルから噴き出され、切断を助ける役割を果たします。アシストガスは、融解した金属を除去したり、燃焼作用を促進したりするために使用されます。
目的に応じて光学系とガスノズルを一体化させた加工ヘッドも有用です。加工部位の様子をモニタするためのカメラやパワーメータを取り付けられるものも市販されています。
さらに、スキャナーやコンピューターの制御装置もレーザー切断システムに組み込まれ、照射位置の制御や切断プロセスの最適化が行われます。
これらの工程が組み合わさることによって、効率的で正確なレーザー切断が実現されます。
2)切断加工に適したレーザーとは?
切断加工に適したレーザーとしては、ファイバーレーザー、YAGレーザー、CO2レーザーなどがあります。それぞれのレーザーは異なる特性を持っており、目的に合わせてレーザーの出力とパルス特性を最適化することが重要です。
ファイバーレーザーは、金属や樹脂など幅広い材質に適当でき、ハイパワー化も進んでいます。ただし、ガラスなどの透明体には光が透過してしまうため、切断加工には不向きです。一方金属素材にはよく吸収され、アルミや真鍮など高反射材で効率よく加工できます。
YAGレーザーもファイバーレーザーと同様、金属やセラミックスなどの硬い材料の切断や穴あけに適しています。また、高いビーム品質を持ち、微細な加工も得意です。
CO2レーザーは、気体の炭酸ガスを媒質として使用します。ファイバーレーザーやYAGレーザーが利用できないガラスを含む幅広い素材に適用でき、導入コストが比較的安価なのが特徴です。ただし媒質であるガスは供給が必要で、ランニングコストを考慮しなければなりません。また反射率の高い金属の加工には不向きです。
3)レーザー切断を実行する際の注意点
レーザー切断を実行する際には、安全管理が非常に重要です。
使用されるレーザーのクラスに応じた対策を行い、適切な保護メガネや防護盾を使用します。
また、レーザーの反射や散乱に対する対策も重要です。適切な反射防止装置を使用して、周囲への被害を最小限に抑えるようにします。
さらに、アシストガスの取り扱いや保管にも注意が必要です。ガスの種類や、流量、方位は、加工品質やランニングコストに大きく影響します。使用時のみならず、保管においても環境条件に配慮して、適切な取り扱いを徹底しましょう。レーザー切断を行うためには、十分な安全対策を講じることが重要です。
難素材も高品質に加工可能!レーザー切断の実例
レーザー切断は、非常に優れた切断品質を実現する加工方法です。特に、難素材の加工や加工の高品質化においては、その高い能力が発揮されます。そのようなレーザー切断の実例について、当社の取扱商品などを参考にご紹介いたします。
1)CFRP(炭素繊維複合材料)
炭素繊維複合材料は、航空宇宙産業をはじめとする産業用途から、スポーツ用品や消費財まで、広く利用されています。高強度の炭素繊維を樹脂に組み込んで作られた材料は、炭素繊維とマトリックス樹脂の材料特性が大きく異なるため、切断や加工が難しく、熱処理には炭化のリスクが発生します。
当社のTru Pulseパルスファイバーレーザーは、高いピークパワーと短いパルスを持っており、マトリックスを過度に焦がさずに炭素を気化させることができます。材料に穴を開けたり、特定の部分に加工を施したりするための、技術とプロセスパラメーターが開発されました。
参考:JLCレーザー加工サイト「炭素繊維複合材料のマイクロマシニング」
2)金属箔
リチウムイオン電池は、電話やパソコン、そして電気自動車のような、さまざまな場所で広く利用されています。特に自動車業界では、電気自動車の普及に伴い、今後数年で電池の需要が大幅に増加する見込みで、電池の開発競争も活発です。そのため、製造プロセスは需要に柔軟に対応する必要があります。
リチウムイオン電池は、セルに密に詰められた、電極がコーティングされた箔で構成されています。この箔は、アルミニウムや銅などで作られており、カソードとアノードの役割を果たします。
金属箔は、陰極のリチウムベースの酸化物で覆われています。通常、箔の厚さは0.008〜0.015 mmほどですが、コーティングを施すことで、材料の総厚さは0.2 mmを超えることもあります。従来の方法では、メカニカルカッターなどを使用しており、箔に損傷が生じたり切断品質が低下したり、繰返しの使用で刃が鈍くなる可能性がありました。また、刃を交換するためには、プロセス全体を停止する必要もありました。
しかし、TrumpfのTru Pulseシリーズは、ランニングコストを最小限に抑えつつ一貫した切断結果を実現し、事実上メンテナンスフリーな性能を発揮します。
さらに、ガルバノメータースキャナーと組み合わせることで、他の材料を傷つけることなく、型にはまらない形状の切断が可能な非接触のシステムが構築可能です。
参考:JLCレーザー加工サイト「リチウムイオン電池用箔の切断」
3)金属やセラミックの微細切断加工(セラミックの切断)
窒化アルミニウム(AlN)は、多くの有益な機械的特性を備えた産業向けの素材です。窒化アルミニウム(AlN)は、エンジニアリングセラミックの中で最も高い熱伝導率をもつ素材の一つで、また熱膨張係数はアルミナのおよそ半分です。
AlNセラミックは、これらの特性により、エレクトロニクス業界で広く使用されており、特にヒートシンクとしてよく活用されています。しかしながら、AINは硬くて脆いため、従来の機械加工方法では処理が困難とされていました。
Tru Pulse シリーズは、ロングパルスと低いスキャン速度を使用して、高品質のエッジ仕上げを実現します。このアプリケーションでは、低い熱伝導特性により、光エネルギーの過剰な吸収を抑えられ、素材の溶融や気化が発生しません。
Tru Pulse シリーズ 高出力ファイバーレーザーの仕様により、エッジ品質を損なうことなくプロセス時間を短縮できます。また、材料を焼成する前に、AlNセラミックを緑色の状態で切断することも可能です。
このプロセスは非常に高品質な切断を実現しますが、品質をさらに向上させるためには、後処理が推奨されています。また、セラミックの穴あけや彫刻も同様に、高品質かつ効果的な処理が可能です。