基板用 高速レーザー欠陥スキャナー PrimaScanシリーズ
Onto Innovation (旧Lumina Instruments)
基板用高速レーザー欠陥スキャナー PrimaScanシリーズ。ガラス基板、半導体基板、ディスプレイ基板などの基板の欠陥を可視化する欠陥検査イメージング装置です。 高速での測定とnm単位の高いPSLパーティクル感度を実現。透明、半透明、不透明の基板に対応。サンプルの大きさから PrimaScan、PrimaScan R&D、PrimaScan Pをラインアップ。最大サンプルサイズ600mm x 600mmに対応。ウエハ入荷検査、ウエハチャックの検査。ブランケットフィルム(膜付きウエハ)の検査。AR/VR/MR用マイクロレンズアレイの内部応力・ギャップ等の検査。フォトレジストのコーティング欠陥検査などに使用いただけます。
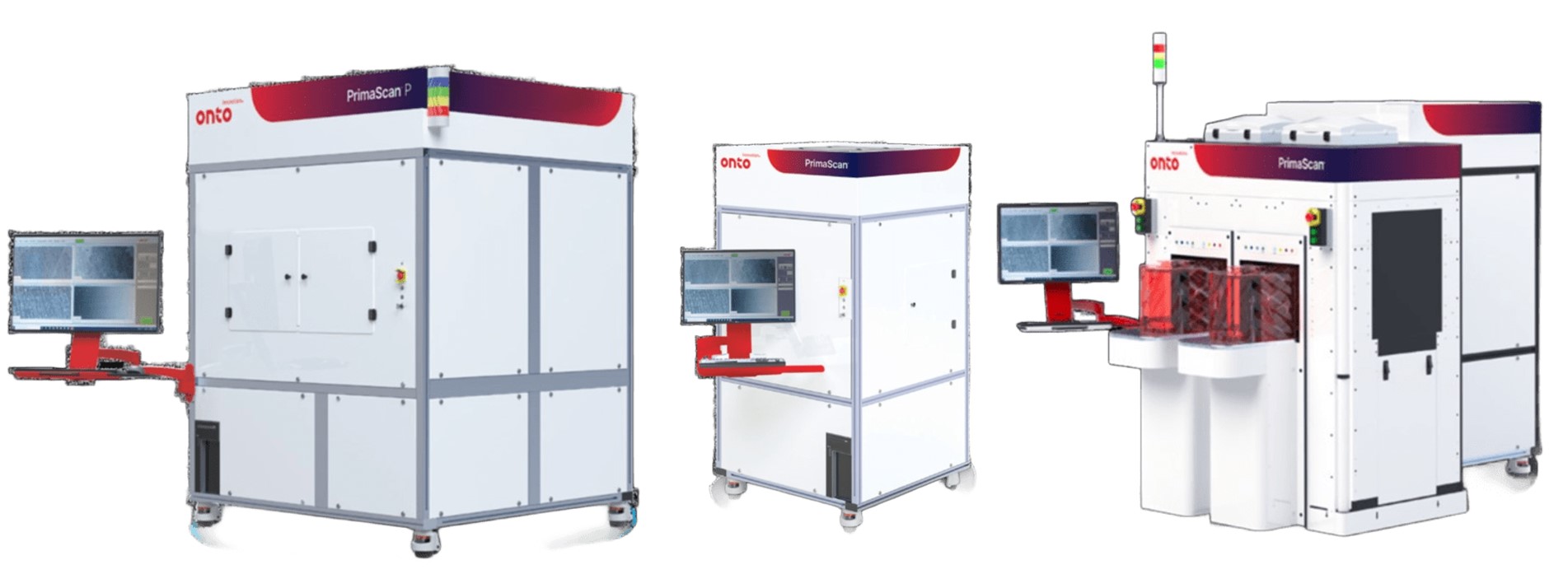
基板用 高速レーザー欠陥スキャナー PrimaScanシリーズ とは
基板検査装置「PrimaScanシリーズ」は、透明、半透明、不透明な基板の全面欠陥検出、マッピング、および分類・レビューを行う光学検査システムです。同時動作の4つの検出チャネルと独自の検出技術を利用することにより、半導体基板やハイテク向けガラス基板の歩留まり制御とプロセス管理を強化します。レーザースキャン方式でありながら非常に高速で、様々なサイズ、形状、厚さの基板を搭載することが可能です。
基板用高速欠陥イメージング装置 PrimaScanシリーズ の特長
- レーザースキャン式(非回転式)
- 矩形、薄い基板、反り基板、特殊形状の基板を検査可能
- サブナノメートルスケール膜欠陥
- 欠陥の検出、クラス分け
- 透明および不透明の基板に対応
- 最大サンプルサイズ600mm x 600mm
PrimaScanシリーズ 各種
基板検査装置 PrimaScanシリーズの 4つの検出チャネル
![]() | ![]() | ![]() | ![]() |
偏光 | 反射率 | 表面傾斜 | 暗視野 |
![]() | ![]() |
![]() | ![]() |
高速欠陥イメージング装置 PrimaScanTシリーズの各機能
- Defect Map: 欠陥種類に応じた色別表示
- Pareto Chart: 欠陥種類と合計数
- Defect Summary:欠陥サイズや膜厚に基づく欠陥のビニング、グループ化
- Report: 欠陥の種類、場所、長さ、サイズなどをレポート(CSVフォーマット)
- Zoom: 指定した欠陥を画像で表示・レビュー
関連非接触測定 膜厚測定(厚み計)・3D測定イメージング
PrimaScanシリーズ 応用例
- ブランケット誘電体または金属欠陥検査
- マイクロ流体におけるガラスのコーティング厚さの変化
- 単層有機残留物
- ウエハチャック汚染
- AR/VR/MR用マイクロレンズアレイの内部応力、エアギャップ、接着剤のオーバーフロー(CISを含む)
- 透明なボイド 空隙( フィルム、ウエハ、接着ウエハ)
- 平面な光学部品の異物混入
- ヘイズ検出と計測
- ウエハの受入品質検査
- フォトレジストコーティングの欠陥
- フォトマスクブランク欠陥と表面汚染
- ポストグラインド/TAIKOウエハ(またはフィルムフレーム)の欠陥
- ゲルパック、ワッフルパック、JDECサンプルトレイのサンプル検査
- 未パターンガラスパネルの入荷品質検査
- ブランケット誘電体またはメタリック塗装パネル
- ガラスの膜厚ばらつき
- 単層有機残留物
- フォトレジストコーティングの欠陥
- パネル全体の応力と誘起点応力
- TGV形成検査
- ガラスパネルウエハエッジチップ
- ヘイズ検出と計測
- 高反り/反りウエハのハンドリングと測定
基板用高速欠陥イメージング装置PrimaScanシリーズ の 検出事例
ガラス基板でのしみの検出
しみや有機残留物は、洗浄プロセスによる汚染または残留物による表面の変色です。これらは基材へのコーティングの接着にも影響を与える可能性があります。
サンプル: 150mm幅ガラス基板. 画像: 全体画像 (左) 、拡大画像47mm x 70mm (右)
右の拡大画像ではガラス基板の上面と底面のしみを見ることができます。暗部:上面のしみ、明部:底面のしみ
サンプル: 150mm幅ガラス基板 画像: 全体画像 (左) 、拡大画像73mm x 48mm (右)
拡大画像で見えているのは、ガラス基板の洗浄工程で発生した不純物が付けた特有のしみ
ガラス基板での残留応力の検出
残留応力は製造中にガラスおよびガラスセラミック材料内に形成される張力または屈折率の変動によって引き起こされます。これは、ストリエーション、内部欠陥、および表面トポグラフィーの変化につながる可能性があります。また残留応力は材料の機械的特性に影響を与えることも知られています。
サンプル: 150mm幅ガラス基板 画像: 全体画像(左) および拡大画像 15 mm x 8 mm (右)
ビームはサンプルを通過し、底面で反射します。拡大画像で見られるのはガラス内部の張力によるものです。また左の線は屈折率の変化によるものです。
ガラス基板の表面の粒子の検出
ガラスの表面の粒子は、様々な原因の可能性がありますが、通常は洗浄または梱包段階で発生します。 L本システムは、ガラス表面で150nmまでの粒子を検出できます。粒子の発生・付着を管理することは、高品質と歩留まりを達成するために重要です。粒子を特定し、製造プロセスの早い段階で対策を講じることができれば、下流プロセスでのリソースの浪費することを回避することも可能です。
画像は、ガラス基板の上に散在するPSL球体の集まりで、最小150 nmの粒子を検出・分類するスキャナーの校正に使用されています。
PSL球体の2つの集まりがガラス面の上にあります。各々のシステムはPSL(Polystyrene Latex)球体を使って校正されます。ガラス上ではPSL粒子の感度は150nmです。
ガラス基板の内部の介在物、表面の粒子の検出
介在物は溶融段階でガラス内に取り込まれた汚染物質の結果です。 これらは、基板の光学的および機械的特性に影響を与える可能性があります。本システムではガラス表面の粒子と内部の介在物を区別して検出することができます。
サンプル:150mm幅ガラス基板
粒子・介在物と色分けされ、Defect Map(欠陥マップ)に表示されます。
ガラス基板の傷の検出
傷(スクラッチ)は、製造段階、洗浄段階、またはガラスの乱暴な取り扱いが原因で発生する可能性があります。 また、多層構造の場合は内部に傷が発生する場合があります。 スクラッチはガラスの外観および機械的特性に影響を与えます。
サンプル:100mm角のガラス 画像 30mm x 50mm
サンプル :3層構造のARレンズ 拡大画像 10mm×15mm 上面(左)と内面(右)
一度目のスキャンで上面の粒子や外部の傷をイメージングし、2回目のスキャンでガラス基板内部の傷と表面より0.5㎜下の内部欠陥をイメージングします。
ディスプレイ基板の局所的な膜厚変動のイメージング
Films on Glass ガラス上のフィルムのわずか数オングストロームの局所的な膜厚変動を分析できます。 ガラス上のフィルムや、ITO表面に存在する汚染物質を検出します。フィルムの不均一性や汚染物質は、ディスプレイの性能や外観に悪影響を及ぼす可能性があります。
数オングストロームの局所的な膜厚変化も容易に捉えることができます。右側に見られるような汚れの残りなどの基板欠陥が原因であることもあります。
イメージセンサの表面欠陥の検出
カバーガラス上とイメージセンサ上の両方の表面の欠陥を検出して分類します。
カバーガラス越しにイメージを取得し、イメージセンサー表面の欠陥を測定することが可能です。
半導体基板のコーティング欠陥の検出
不適正なプロセス条件や基板の洗浄不足により基板コーティングに欠落が発生します。これらの欠陥により、パフォーマンスの低下や、その後の歩留まりの低下が発生する可能性があります。
サンプル: 100mm幅シリコンウエハー: 全体画像 (左) 、全4チャネルの拡大画像 3.5 mm x 2 mm (右)
暗視野と偏光チャネルを比較することで、散乱計として、またフィルムの欠陥検出ツールとして機能します。
半導体基板のフィルムコーティングの均一性の検出
フィルムの欠陥の領域が大きくなると、フィルム層またはコーティングの品質が損なわれ、フィルムの均一性に問題が生じる可能性があります。 本システムでは従来の顕微鏡観察では不可能であった、より包括的な観察が可能です。
サンプル: 銅コーティングをした100㎜シリコン基板 : 拡大画像 偏光(左)、傾斜 25 mm x 30 mm (右).
シリコン基板の上に銅のコーティングが不均一に分布している。これが、顧客が特に関心を寄せるたメッ網目状のネットワークを生成していた。
サンプル: 自己組織化単分子膜(SAM) 拡大画像 38 mm x 27 mm
赤と黄色の部分は、自己組織化単分子膜(SAM)上で単分子膜の分子がシリコン基板と強く相互作用していない箇所を示しています。
PrimaScanシリーズ 製品PDF
PrimaScan (300㎜ x 300㎜対応)製品PDF (準備中) | PrimaScan R&D (450㎜ x 450㎜対応)製品PDF | PrimaScan P (600mm x 600mm対応)製品PDF |
![]() | ![]() | ![]() |
基板欠陥 PrimaScanシリーズの仕様とメリット
- 4つの検出チャンネル
– 偏光、スロープ、BF(明視野)、DF(暗視野) - 全表面スキャン(FS/BS/Edge)とサブナノメーター感度のイメージング
- 粒子欠陥(≥90nm PSL)/表面汚染(≥5Å)
- FS/BS同時検査(透明・半透明基板のみ・基板のみ)
- 内部欠陥(介在物など)の深さをレポート
- 内部応力または屈折率変化の検出
- 動的な反り補正
- 薄型(≥100μm)および厚型(≤7mm)ウェハ/基板に対応
- 基板ハンドリング
- 複数のハンドリングオプション
– ウェハ、フォトマスク、フィルムフレーム、JDECトレイ、ワッフルパック - 複数のロードオプション
– マニュアル、オープンカセット、SMIF、EFEM - 画像ベースの自動欠陥分類機能
- オンラインおよびオフラインレビュー機能